Tubing, also called an electric tubing is a hollow cylinder with a flexible exterior that is used for transporting liquids or to enclose electrical or optical cables. These tubes are normally used for conducting electrical current. Tubes are commonly found in large industrial facilities such as power plants, dams and water plants.
Tubes can also be used in smaller applications like gas line and water line
They are commonly made from PVC and polyvinyl chloride. They are also available in flexible, flat and rigid tubes. You can choose between rigid and flexible tubes depending on your application needs.
Flexible tubes are flexible tubes that are made of a flexible material such as plastic or rubber. This material is able to mold into the shape of whatever you want it to fit. On the other hand, the rigid tubes are made of more solid materials and are very stable. In order for a rigid tube to be able to support the load it will be receiving from its surroundings, it is able to be bent, rolled or even folded. This type of tube is commonly used in industries where you need a large number of tubes at different lengths.
Because of their flexibility, flexible tubes are very useful in places where you need a large number of tubes in one area. Examples of these industries include petroleum refineries, power stations and water and gas line distribution networks. These tubes are also popularly used in laboratories, chemical laboratories and food processing facilities. In these types of industries, flexible tubes are the best option because they are able to be used for more purposes and they are more resistant to any damage caused by heavy-duty equipments.
While the rigid tubes are more expensive than the flexible ones, they are also more durable and resistant to damage. They are also better able to carry out specific applications. The only problem is that they are more bulky and difficult to install. For this reason, they are usually placed inside factories where they are not easily seen.
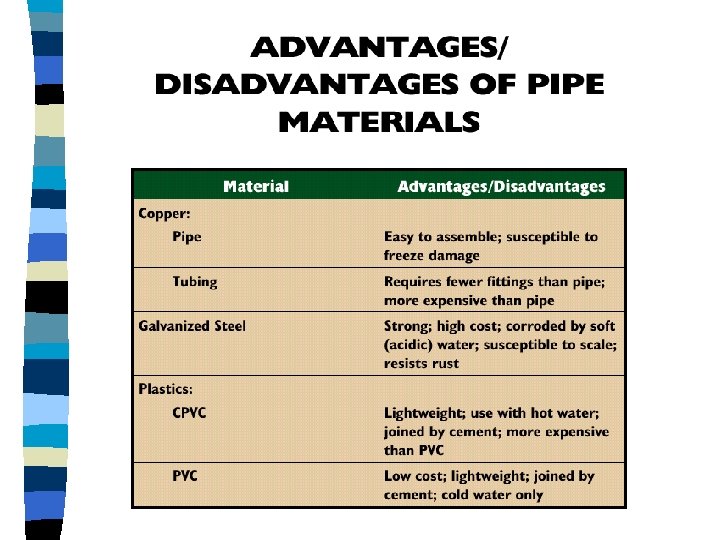
Some of the advantages of using a flexible tube over the rigid one include: flexible tubes are more flexible tubes can be bent, rolled and folded to fit any type of applications. They are also more cost effective because they require less labor for installation and less equipment to be installed. Also, flexible tubes are much lighter and more convenient compared to rigid tubes. They also have many different shapes, sizes, so they are more convenient when it comes to installation. Moreover, they are often easier to transport and move around compared to rigid tubes.
Flexible tubes are also preferred because they are more flexible tubes are also flexible when being stored. Also, they are more resistant to any damage caused by heavy-duty equipment like motors, which are found in the power station. They are also easy to install and can be rewired easily.
Another advantage of using flexible tubes is that it can be reused
They can be reused many times over, which means that you will not need to buy more equipment to store them. There are no chemicals to clean and they are also easy to install and repair unlike rigid tubes.
Flexible tubes are also very strong and durable, which makes them easy to install. They can also withstand extreme heat and pressure, making them highly suitable for certain applications.
The disadvantages of using a flexible tube are: Since it is not as versatile as the rigid one, flexible tubes may not be able to cope with different applications and they may not be able to handle certain situations. The flexible tubes are also not able to bend and twist as well. In the manufacturing industry, they are often used for manufacturing purposes.
There are also disadvantages of using the flexible tubes, but then again there are many benefits too. This article aims at showing some of the advantages and disadvantages of using these tubes in the industry. Before buying flexible tubes or buying a particular brand, make sure that it is flexible, cost effective and durable.